H2S Monitor Calibration: Ensuring Safety and Compliance
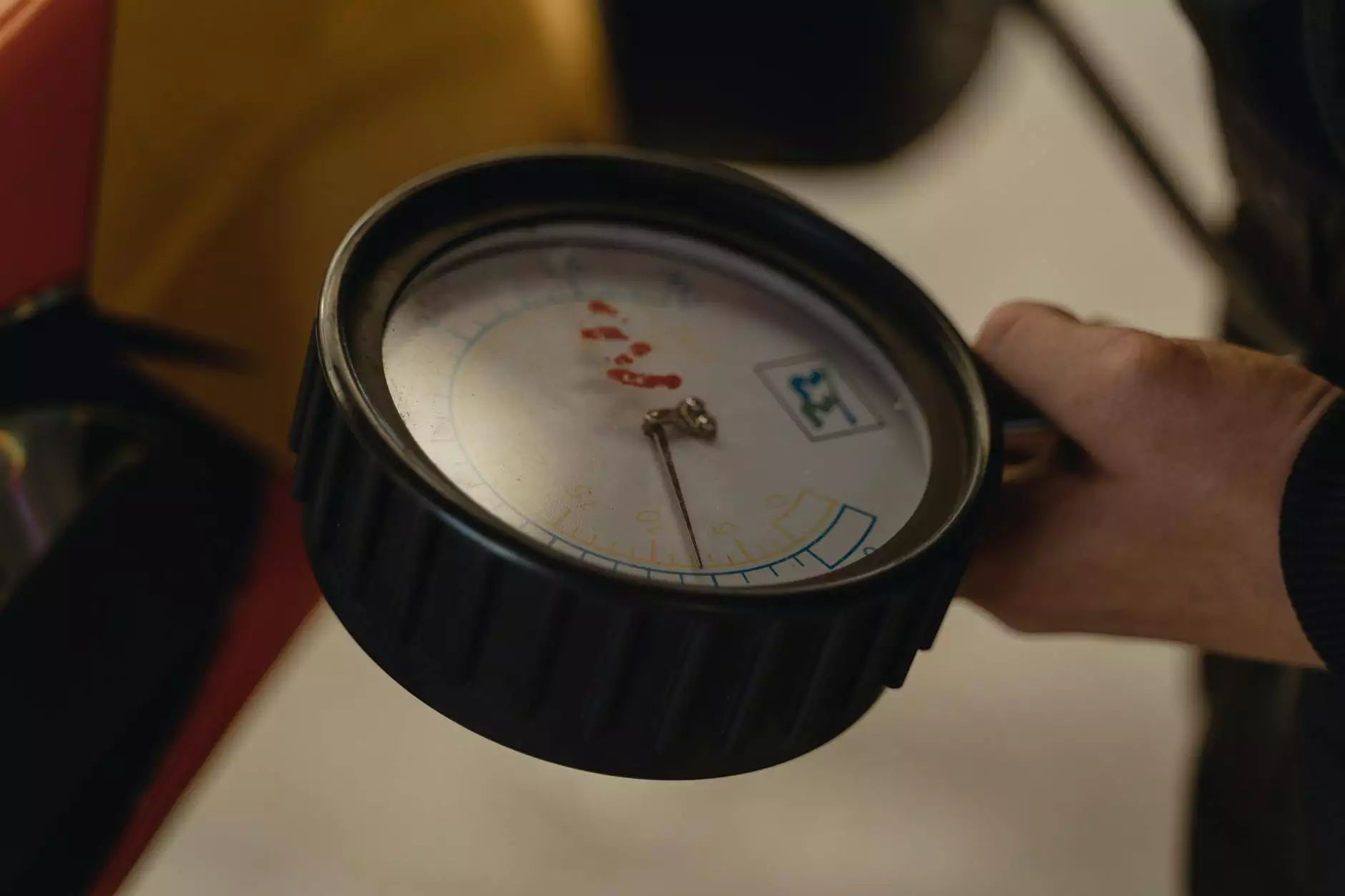
In an era where workplace safety is paramount, H2S monitor calibration has become a vital process for organizations that deal with hydrogen sulfide (H2S) gas. This management practice ensures that monitoring devices read accurately, thereby safeguarding both personnel and regulatory compliance within various industrial settings. This comprehensive guide delves into everything you need to understand about H2S monitor calibration, its significance, and best practices to implement for optimal safety.
Understanding Hydrogen Sulfide (H2S)
Hydrogen sulfide is a colorless gas known for its recognizable rotten egg smell. While it is naturally occurring in certain environments, such as sulfur springs and volcanic gases, it can also be released during various industrial processes including:
- Oil and gas extraction and refining
- Wastewater treatment
- Pulp and paper production
- Food processing
Due to its toxicity and flammability, understanding H2S and properly calibrating monitors is crucial for ensuring worker safety and minimizing environmental impacts.
The Importance of H2S Monitor Calibration
Calibration is the process of adjusting the output or indication of a measuring instrument to agree with the value of the applied standard. In the case of H2S monitors, calibration is essential for several reasons:
- Accurate Readings: A calibrated H2S monitor provides accurate readings, allowing for timely warnings of gas presence.
- Regulatory Compliance: Many industries are required to comply with OSHA and other regulatory standards, which mandate appropriate monitoring of hazardous gases.
- Worker Safety: Accurate sensors protect workers by providing early detection of H2S gas, preventing dangerous accidents.
- Equipment Longevity: Regular calibration can extend the lifespan of monitoring devices by ensuring they operate correctly.
Calibrating Your H2S Monitor: The Process
The calibration of H2S monitors generally follows a systematic procedure. Here we outline a comprehensive calibration process that should be adhered to for optimal results:
1. Understanding Calibration Standards
Before you begin, familiarize yourself with the manufacturer's specifications for your H2S monitor. Different models and brands may require specific calibration gases and techniques.
2. Prepare Calibration Equipment
You will need:
- H2S calibration gas with a known concentration
- Calibration kit, including a regulator and inlet tubing
- A clean environment to avoid cross-contamination
3. Testing the Monitor
Prior to calibration, test the monitor in normal operation to ensure it is functioning correctly. This step should help identify any major deviations in readings.
4. Zero Calibration
Using clean air (0% H2S concentration), adjust the monitor's output to read zero. This step is crucial for establishing a baseline from which measurements will be taken.
5. Span Calibration
Introduce the calibration gas to the monitor at a predefined concentration. Adjust the reading to match the known value of the calibration gas. Follow the manufacturer’s guidelines related to exposure time and maximum level.
6. Document the Calibration
Keep detailed records of all calibration results, including date, concentrations used, and the technician’s signature. Documentation is essential for compliance purposes and future reference.
Best Practices for H2S Monitor Calibration
To ensure the effectiveness of your H2S monitor calibration processes, consider the following best practices:
- Regular Calibration Schedule: Establish a routine calibration schedule based on the manufacturer's recommendation and the workplace environment.
- Training Personnel: Ensure that staff responsible for calibration are properly trained to monitor gas levels and understand calibration procedures.
- Use High-Quality Calibration Gas: Utilize calibration gases that have a known certification and consistency for accurate readings.
- Check for Calibration Drift: Regularly assess monitors' performance between calibrations to catch any discrepancies early.
- Rapid Response to Alarms: Staff must be trained to respond to monitor alarms promptly, ensuring swift action in potentially dangerous situations.
Common Issues in H2S Monitor Calibration
Even with stringent calibration procedures, issues can occasionally arise. Here are common problems and suggested solutions:
- Calibration Drift: Monitors may drift over time due to environmental factors. Regular checks can help minimize this issue.
- False Alarms: Dust or chemical residues can affect readings. Keeping the monitor clean is essential.
- Inverted Readings: Occasionally, monitors could display inverted values if calibration is done improperly. Always follow calibration steps meticulously.
H2S Monitoring Solutions Available
Several types of H2S monitors can be utilized depending on specific needs:
- Portable Monitors: Ideal for personal safety, these monitors can be taken into the field and are essential for workers in hazardous locations.
- Fixed Monitors: Installed in stationary locations, these devices continuously monitor air quality in environments where H2S gas is prevalent.
- Multi-Gas Monitors: Capable of detecting various gases, these devices offer a comprehensive solution for environments susceptible to multiple toxic gases.
Conclusion: Prioritizing Safety with H2S Monitor Calibration
As industries continue to evolve and engage with potentially hazardous substances, the calibration of H2S monitors becomes indispensable. By understanding the calibration process, best practices, and common challenges, organizations can better protect their workers and comply with industry regulations. Being proactive in maintaining accurate H2S monitoring is not just a regulatory obligation; it is a moral imperative to ensure the safety and wellbeing of all personnel.
If you're looking for further information or training on H2S monitor calibration, visit h2sonlinetraining.com for detailed resources and courses to enhance your knowledge and compliance.