Understanding Die Casting Parts: A Comprehensive Guide
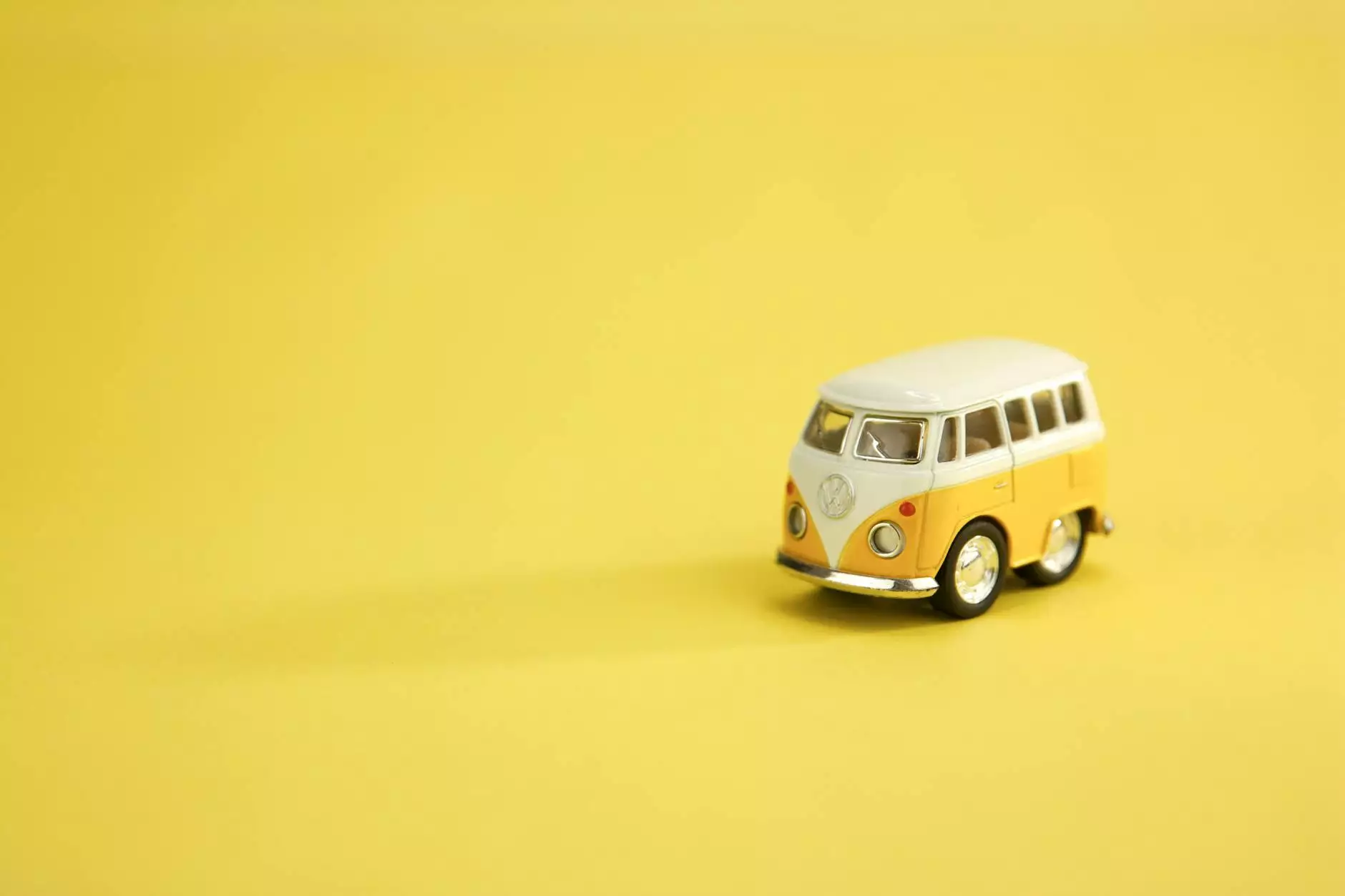
Introduction to Die Casting Parts
Die casting parts play a crucial role in modern manufacturing, providing precision and cost-effective solutions for various industries. This article delves deep into the nature of die casting parts, their manufacturing processes, advantages, applications, and why they are essential for businesses looking to enhance their production capabilities.
What are Die Casting Parts?
Die casting is a metal casting process that forces molten metal into a mold cavity under high pressure. The molds, known as die casting dies, are typically made of steel or iron and are designed to create intricate shapes and features. The process is primarily used for producing die casting parts in various industries, including automotive, aerospace, consumer goods, and electronics.
How Die Casting Works
The die casting process consists of several critical steps:
- Preparation of the Mold: The mold is pre-heated to ensure proper flow of molten metal.
- Melting of Metal: Alloys such as aluminum, zinc, and magnesium are melted in a furnace.
- Injection of Molten Metal: The molten metal is injected into the mold at a high pressure.
- Cooling and Solidification: After injection, the metal cools and solidifies within the mold.
- Removal: Once solidified, the mold opens, and the die casting parts are ejected.
- Trimming: Excess metal is trimmed off, resulting in the final product.
Types of Die Casting Processes
There are two primary methods of die casting:
- High-Pressure Die Casting: This method uses high pressure to inject molten metal into the mold. It is best suited for large production runs.
- Low-Pressure Die Casting: Here, lower pressure is used, leading to less dense products. This method is often used for larger parts.
Materials Used in Die Casting Parts
The choice of material significantly influences the properties of the final die casting parts. Common materials used include:
- Aluminum: Known for its lightweight and excellent corrosion resistance, aluminum die casting parts are prevalent in automotive applications.
- Zinc: Offers high strength and good fluidity, making it ideal for precision parts.
- Magnesium: Lighter than aluminum, magnesium provides superior strength-to-weight ratios.
- Copper: Used for parts requiring high thermal conductivity.
Advantages of Using Die Casting Parts
The advantages of implementing die casting parts in manufacturing processes are numerous:
- Precision and Accuracy: Die casting provides exceptional dimensional accuracy, reducing the need for secondary operations.
- Complex Designs: Can create intricate shapes and fine details that may be challenging with other methods.
- Cost-Effectiveness: High production rates lower the overall cost per unit.
- Surface Finish: Offers a superior surface finish, often requiring minimal post-processing.
- Material Efficiency: Minimizes waste, as excess material can often be recycled.
Applications of Die Casting Parts
The versatility of die casting parts allows their use in a wide range of applications, including:
- Automotive Industry: Used in engine components, transmission housings, and structural parts.
- Aerospace Engineering: Essential for lightweight structures and components that require strength.
- Consumer Electronics: Employed in producing casings, connectors, and heat sinks.
- Industrial Machinery: Provides critical parts that withstand harsh operating environments.
- Medical Devices: Utilized in precision components where reliability is essential.
The Future of Die Casting Parts
As technology advances, die casting parts continue to evolve. Innovations such as 3D printing are being integrated into die casting molds, allowing for faster prototyping and more complex designs. Additionally, the shift towards sustainability is influencing the materials used, with a focus on recyclable and environmentally friendly substances.
Conclusion
In conclusion, die casting parts are pivotal in contemporary manufacturing. Their ability to combine precision, efficiency, and versatility makes them an invaluable asset across various industries. With the ongoing advancements in casting technology and materials, businesses can expect even greater benefits and applications from die casting in the future.
Contact Us
For more information on how die casting parts can enhance your manufacturing processes, please contact Deep Mould today. Our team of experts is ready to assist you in finding the best solutions for your needs.